Top 10 Lean Tools for Continuous Improvement
Whether to map, model or automate processes, the quality of operational routines is crucial for those who aim for the top of the market. Find out the Lean tools most used by process consultants to end bottlenecks, eliminate waste, and save money.
Lean is a methodology that everyone should be familiar with at this point. Still, many companies still aren’t taking advantage of the tools that Lean provides. This article will briefly cover what Lean is and its benefits, followed by a list of tools that you can use to secure your company’s continuous improvement.
The Lean Methodology promotes the flow of value to the client through two guiding pillars: continuous improvement and respect for people. There are also some principles or steps for its implementation.
It is both a philosophy and a discipline that, in essence, increases access to information to ensure responsible decision-making at the service of value creation.
What is Lean?
The Lean Methodology originated in the Toyota Production System, a system of the Japanese vehicle industry that revolutionized the manufacture of physical goods in the 1950s. It maintains its dominance in manufacturing but has also found new applications in business, helping companies in all industries eliminate waste, improve processes, and drive innovation.
There are two main pillars that Lean uses to drive its methodology: Continuous improvement and the appreciation of people. Let’s dive a little deeper into those two pillars:
Continuous Improvement
When some people think of Lean Methodology, they think of eliminating waste. While it is true that organizations using this method are usually more focused on removing waste, the ultimate goal is value creation.
The cycle of continuous improvement achieved by organizations applying the Lean Methodology helps them differentiate themselves from competitors. They become more agile, humble, and methodical. They encourage their employees to promote a learning mentality and, more specifically, a test mentality.
With the principle of continuous improvement obtained with the Lean method, ideas are tested as many times as necessary before spending money on them. And this is both a path to innovation and a form of risk management.
Valuing your team
Most of the time, the best ideas come from those closest to production/creation and the customer. The Lean methodology takes advantage of that simple fact to empower your team regarding decision-making and strategy.
“Lean thinking” says that people want to do their best job and are motivated to make decisions that optimize their time and talent to create the most value for the customer. This allows the organization to capture the best ideas and fulfill them.
By using Lean Methodology, the organization empowers employees with decision-making autonomy, the opportunity to master their craft, and the purpose (the “why” behind the work) of understanding the value of their efforts. The leader’s role is to set the goal in question and then allow his talented employees to discover the course of action best suited.
The Principles of Lean Management
When incorporating the Lean methodology into a team, managers will use Lean Management. Within Lean Management are five guiding principles:
• Identify value
• Value stream mapping
• Create a continuous workflow
• Establish a pull system
• Facilitate continuous improvement
Identifying Value
Identifying value is as much about finding opportunities as it is about eliminating waste. The first step to lean management is ensuring that your product or service is worthwhile for the customer. By that, we mean that it has to add value without unnecessary features. Anything that is not perceived as useful, important, or worthwhile should be removed from your final product. The solution must be something customers are willing to pay for without all the bloat (as in, it has to be lean).
Value stream mapping
Value stream mapping is a tool that Lean managers use to identify the flow of value. It’s a way of mapping out your company’s workflow, including all the actions and people who contribute to creating and delivering the final product. You can think of this strategy as mapping out all the different streams that lead to a river, identifying which streams bring freshwater (value) and which are contaminated (no value).
Creating a continuous workflow
This principle focuses on each individual stream. It makes sure that work progresses smoothly, preventing any interruptions or bottlenecks that may occur across and within teams. Keeping in line with our river analogy, creating a continuous workflow is like making sure no logs or debris clogs up your tributaries, removing process interruptions and roadblocks.
Developing a pull system
A pull system works by managing workflow to assist teams in delivering assignments faster and with less unnecessary effort. It ensures that new work is only started when there is demand, minimizing overhead and optimizing storage and operation costs. You can think of this principle as small artificial dams that can be used to control the flow of work as needed.
Facilitating continuous improvement
This is by far the most crucial principle of Lean Management. This is what Lean is all about. It refers to various techniques that can help identify what your organization has done and needs to be done, possible obstacles in the way, and how team members can make their workflows more efficient.
Think of this as regularly scheduled maintenance that takes place continuously throughout every workflow. You must include all employees in this process in order to foster a culture of continuous improvement.
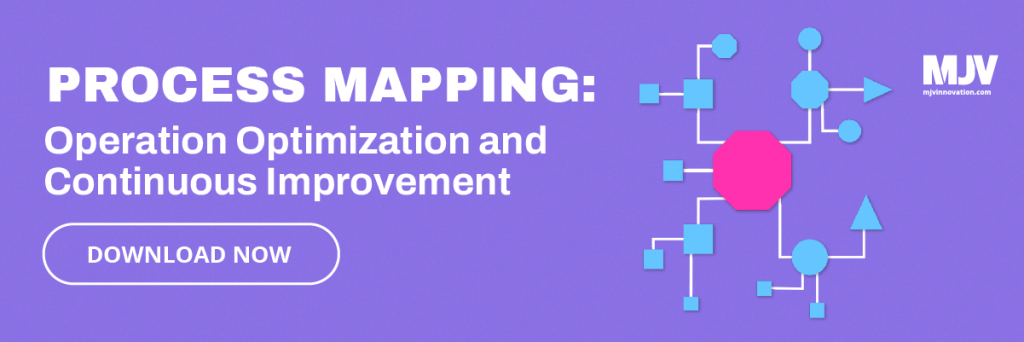
What are the benefits of Lean Management?
Lean Management directly benefits organizations by removing process waste, but its biggest boon comes from the long-term benefits of continuous improvement. This occurs throughout all levels of the organization’s hierarchy and can provide advantages such as:
• A more intelligent business process: The pull system ensures work is only carried out when there is an actual demand and need for it.
• More efficient use of resources: Removing waste ensures that the organization only uses resources when needed and doesn’t spend time and effort on unnecessary tasks and procedures.
• Improved focus: Lean management decreases the number of wasteful activities, allowing employees to focus on tasks that actually produce value.
• Enhanced productivity: Improved focus leads to a more productive and efficient workforce since attention is not given to unnecessary activities.
Combined, these benefits work together to make your company more flexible and give you the ability to address customer requirements in a streamlined manner. It’s a non-invasive way of overhauling your business processes, upgrading your efficiency and product accuracy.
Top 10 Lean Tools to Process Improvement
Now that we’ve touched on the basic principles and concepts behind Lean Management, it’s time to get to what you came here for our list of top lean tools. While these can have various applications in a multitude of sectors, it’s essential to understand where each one will have the most significant impact. Can you use a screwdriver to hammer in a nail? Probably. Should you? Only if you don’t have a hammer.
Remember, this is just a brief overview of each of the lean tools, and this is far from a complete list. If you decide to start using any of these, we recommend committing to further research.
1. 5S
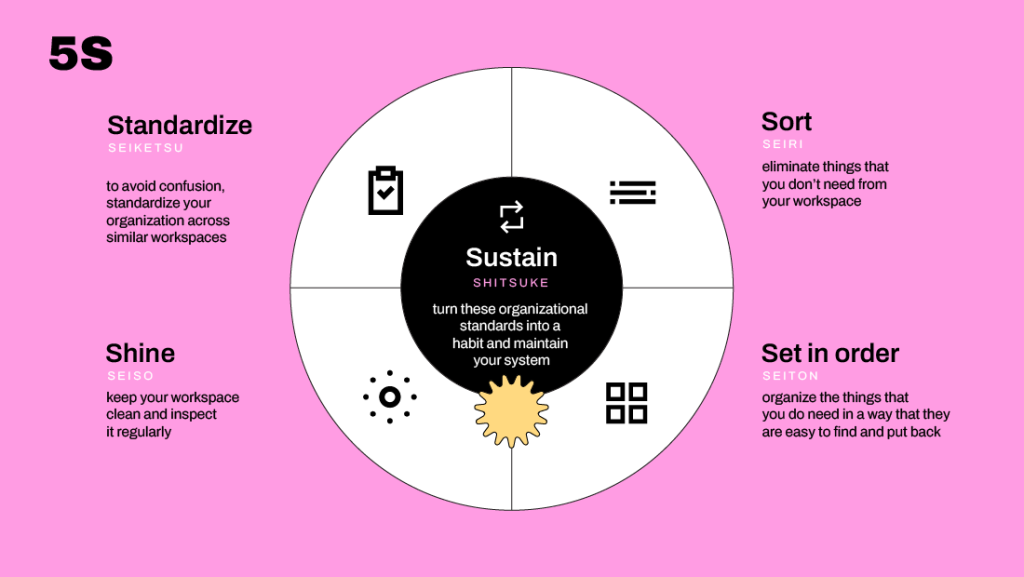
Like the Lean methodology itself, 5S originated in manufacturing and is best suited for cleaning up and organizing workspaces. But just because you don’t use heavy machinery in the office doesn’t mean it can’t be applied to your cubicle. Cleanliness and organization can do wonders for any workspace, whether it’s a factory or a cubicle (or your home).
The five Ss stand for:
• Sort: eliminate things that you don’t need from your workspace
• Straighten: organize the things that you do need in a way that they are easy to find and put back
• Shine: keep your workspace clean and inspect it regularly
• Standardize: to avoid confusion, standardize your organization across similar workspaces
• Sustain: turn these organizational standards into a habit and maintain your system
2. Kaizen
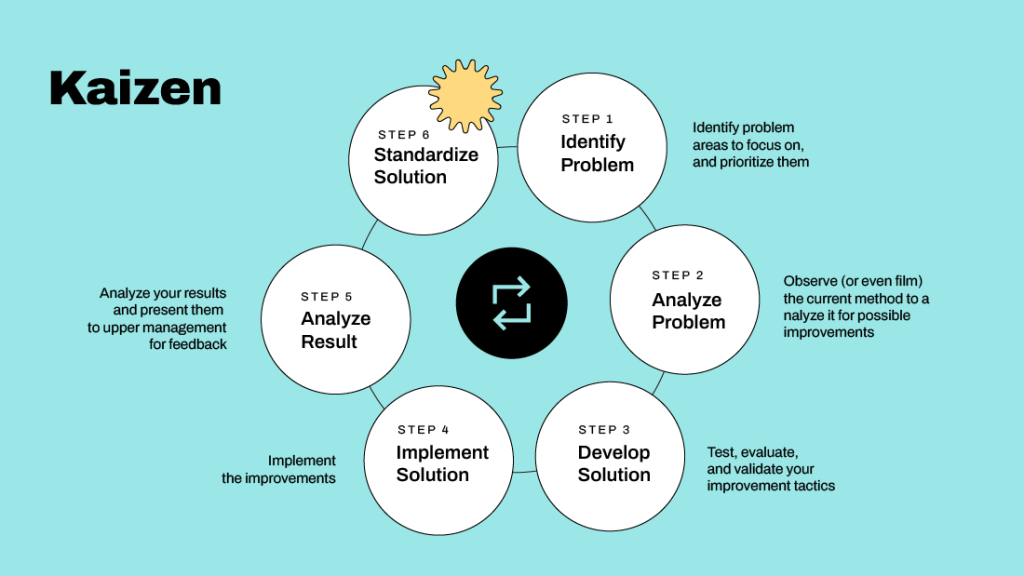
Kaizen is the Japanese word for “continuous improvement” and, as you might have guessed, is the beating heart of Lean Management. We highly recommend including employees from every level and department within your organization. The strategy involves five primary steps:
• Identify problem areas to focus on, and prioritize them
• Observe (or even film) the current method to analyze it for possible improvements
• Test, evaluate, and validate your improvement tactics
• Implement the improvements
• Analyze your results and present them to upper management for feedback
Since there is no such thing as the perfect process, Kaizen can be applied to any department within every company.
3. Single-Minute Exchange or Die (SMED)
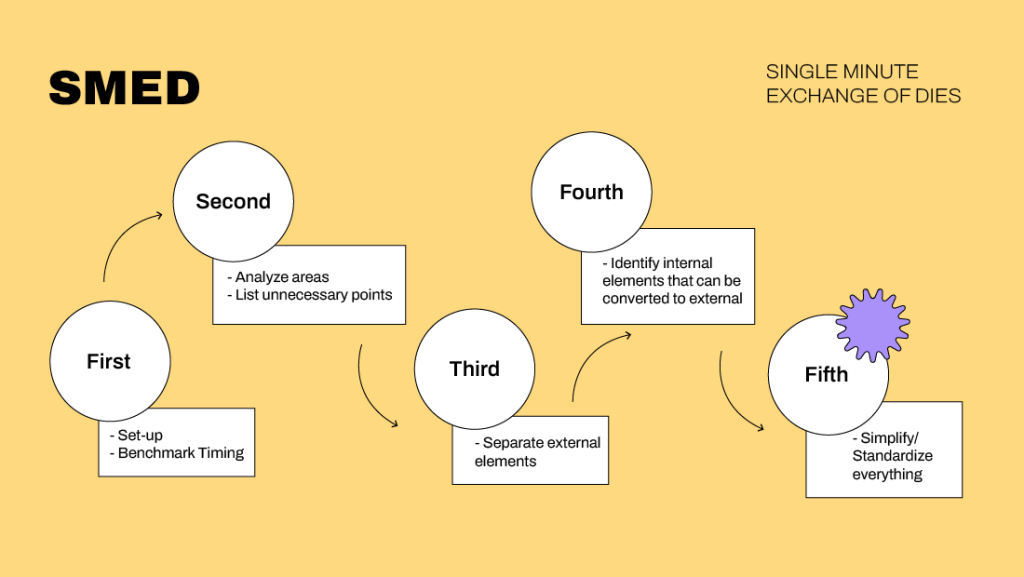
SMED stands for Single-Minute Exchange or Die. Intense, we know. The goal of SMED is to get all changeovers and startups down to 10 minutes.
Each step should take no more than one minute to complete. While this tool was developed for and shines in factories, that doesn’t mean that there isn’t something to take away from this for corporate environments. Meetings, information exchange, brainstorming, all of these activities can be faster and more efficient. Turn unnecessary meetings into emails every chance you get!
4. Value Stream Mapping (VSM)
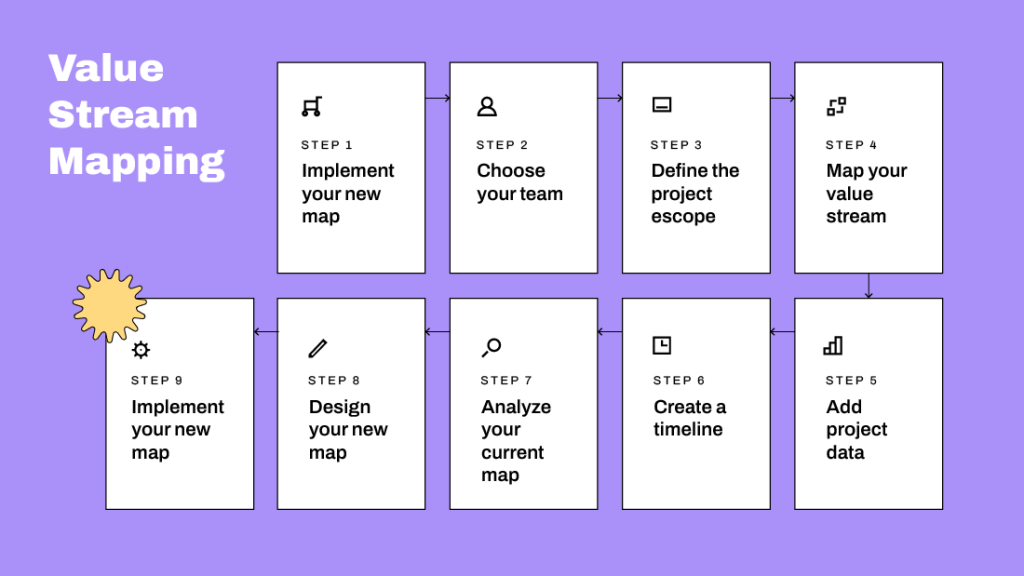
We’ve already touched on this before, but value stream mapping (or VSM) is a tool used by Lean Managers to identify where your product or service value is coming from. It does this through the use of flow diagrams that visually illustrate every step along a process or chain, the people responsible for those steps, and the inputs and outputs for each one. Use it to identify waste, clean processes, and increase efficiency.
5. Bottleneck Analysis
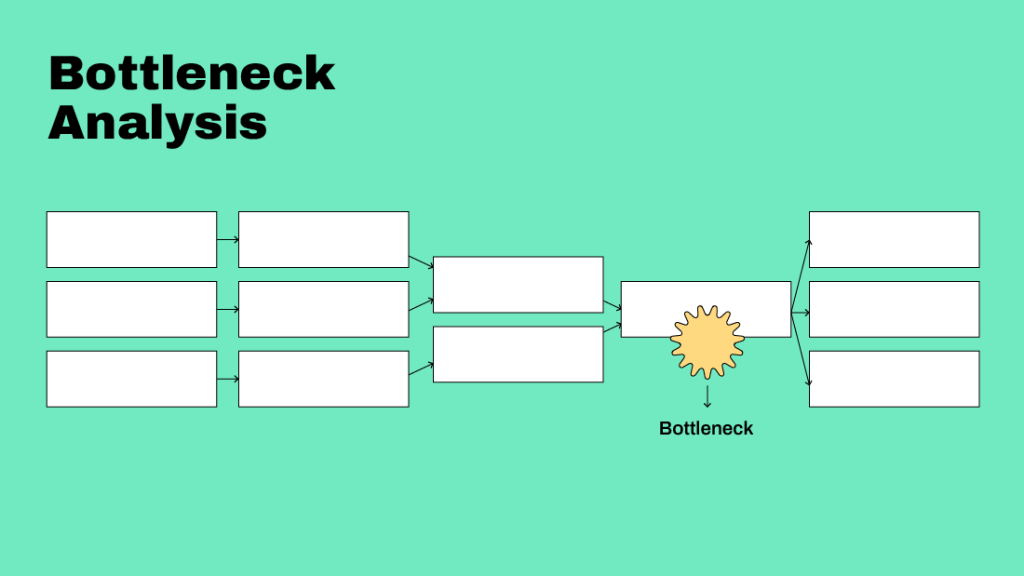
This one is pretty straightforward but incredibly useful. Bottleneck analysis is a structured way of looking at processes and workflows in order to identify where forced downtime occurs, why, and how to fix it. One of the best ways to identify possible bottleneck locations is to simply ask the people involved in the process where they believe bottlenecks lie.
Fixing bottlenecks can be as simple as streamlining your process, but don’t hesitate to increase funding or make new hires when the issue is a lack of resources. It can also be good to prioritize your bottlenecks and focus on solving them one at a time.
6. Plan-Do-Check-Act (PDCA)
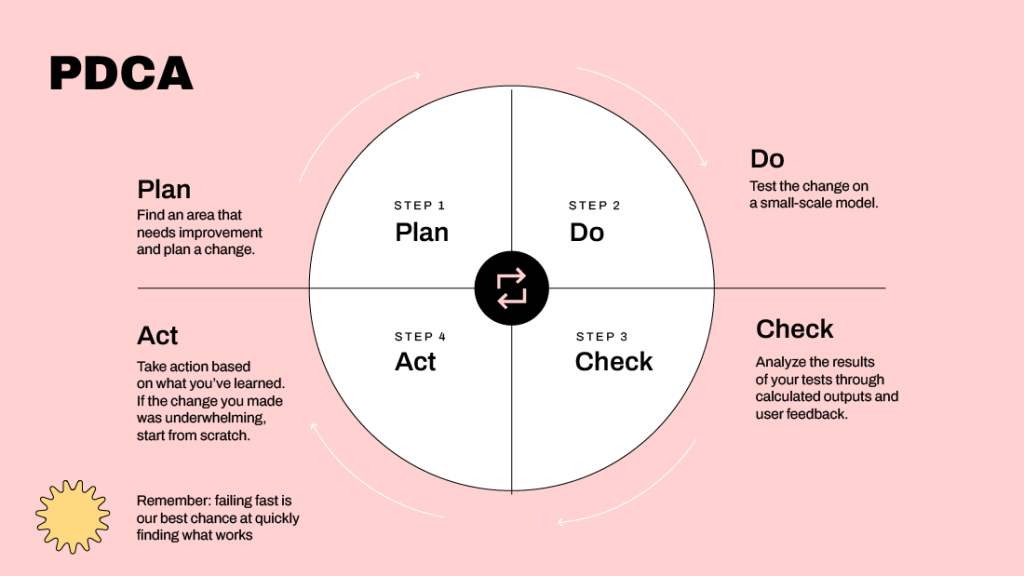
PDCA stands for Plan-Do-Check-Act and is a four-step method for creating and carrying out change within your organization. Like other Lean tools, PDCA is run over and over again in order to facilitate continuous improvement. PDCA is best applied when:
• Conducting an improvement project.
• Designing a repetitive work process.
• Developing a new process or product design.
• Implementing process changes.
• The steps are detailed as follows:
Plan: Find an area that needs improvement and plan a change.
Do: Test the change on a small-scale model.
Check: Analyze the results of your tests through calculated outputs and user feedback.
Act: Take action based on what you’ve learned. If the change you made was underwhelming, start from scratch. Remember: failing fast is your best chance at quickly finding what works.
7. Error Proofing (a.k.a. Poka-Yoke)
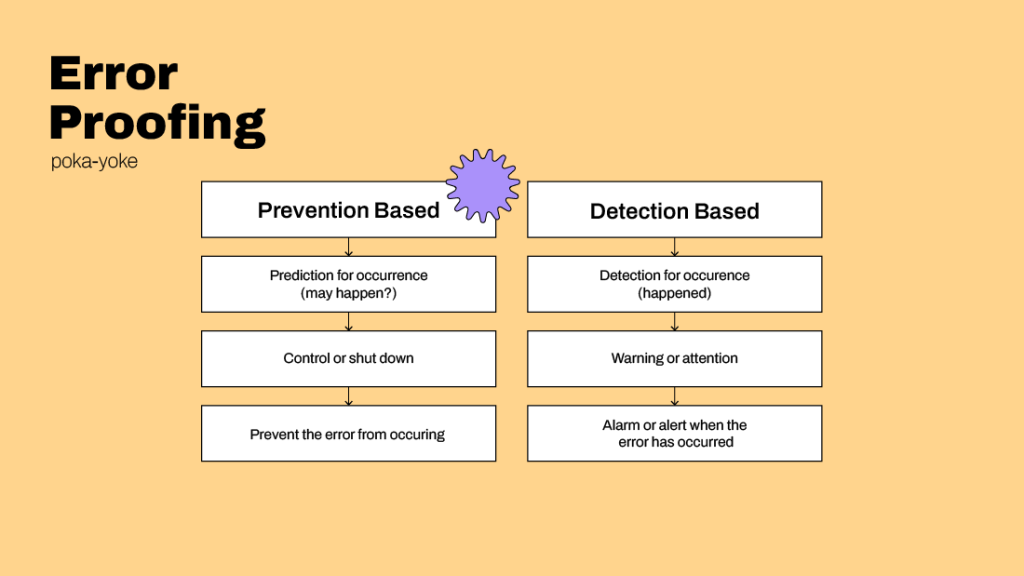
Error proofing, A.K.A. poka-yoke (we’re serious), is a typical process analysis tool that values prevention. Poka-yoke focuses on ensuring the right conditions are met before any process is put in place. This tool provides many of the same benefits as a pull system while also decreasing human error, rework, and inefficiency. Here are a few simple steps you can take to implement error proofing successfully:
• Identify and recognize the issue you are trying to solve.
• Uncover details about how long the problem has been going on and how it is explicitly affecting your process and team members.
• Collect data about the problem and identify as many potential causes as possible.
• Once you have the data, use it to discover the root cause of these problems.
• Decide how to lessen the chances of the problem occurring (we know we’re making this sound simple, but trust us when we say that improvement gets a lot easier with practice).
8. Root Cause Analysis

Root Cause Analysis is a problem-solving methodology that focuses on resolving underlying problems instead of simply applying quick fixes that only treat the immediate symptoms of the pain. A good method of finding these root causes is the “five whys” approach. Like a curious, ignorant child, ask yourself why a problem is occurring and then why that is occurring until you hit a brick wall of problem responsibility.
9. Standardized Work
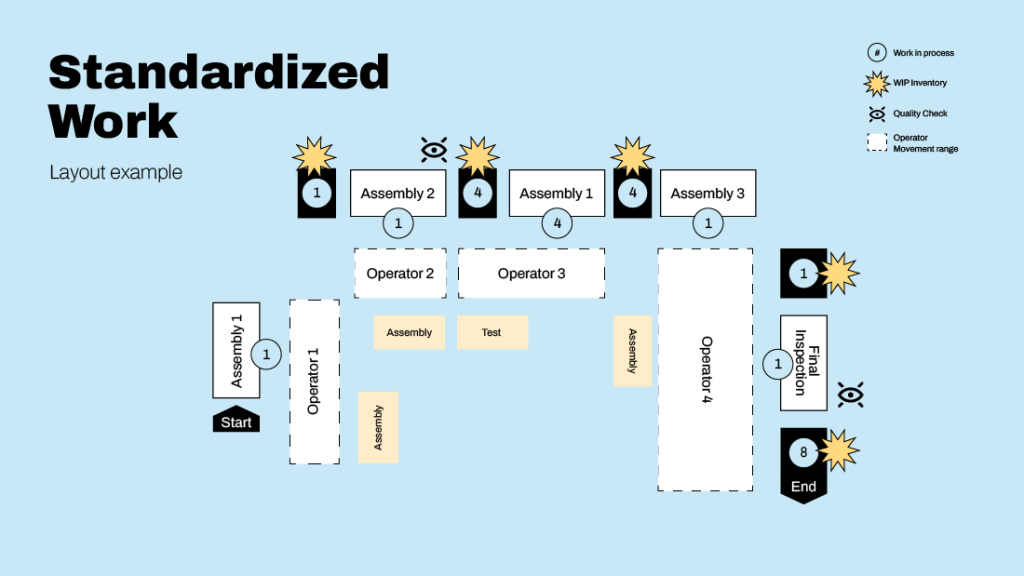
This is another strong, simple tool with a significantly high ROI. It involves detailed documenting of procedures to deduce and capture best practices (as well as the time it takes to complete each task). It should be done on a shared document that is easily changed and accessible. Once the document is created, simply have your team members add to and modify it. It will then become your tutorial on how to do complete specific tasks.
10. Six Sigma
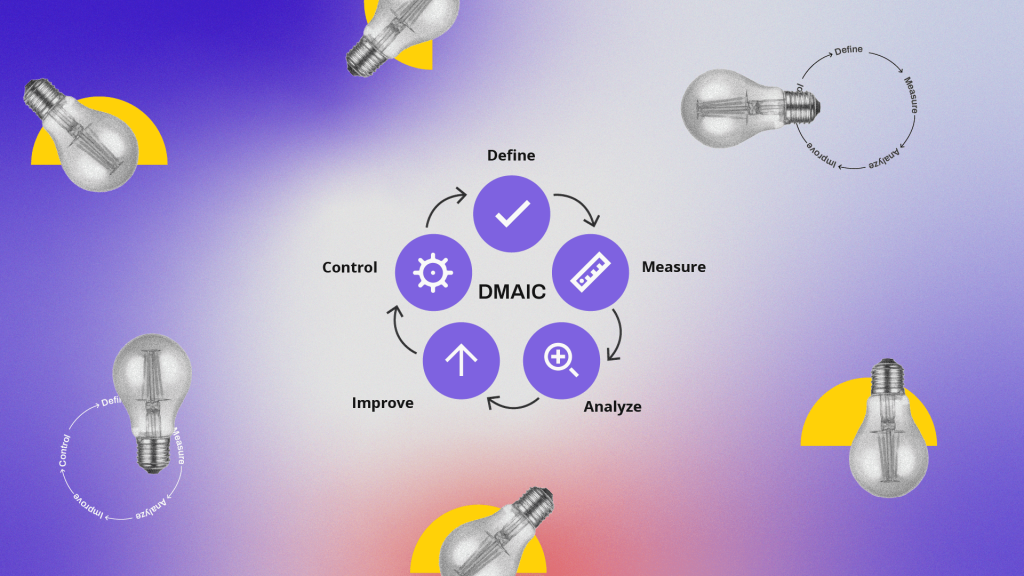
While Six Sigma isn’t exactly part of the “lean tools” set, we thought it would be beneficial to mention it. Six Sigma is another continuous improvement methodology (like Lean!) and offers a strategy for improving processes, reducing waste, and increasing efficiency.
The best part about it is that Six Sigma is actually highly compatible with the Lean Methodology. If you’re interested in learning more about their combination (unsurprisingly titled Lean Six Sigma), have a peek at the ebook we wrote about it here.
A final word on Lean Tools
We hope that this article has helped you understand a bit more about what the Lean methodology and its tools can offer businesses seeking continuous improvement. Information on the subject is everywhere, and at this point, there’s nothing new under the Lean sun. But the last piece of advice that we’d like to share is about Lean implementation.
If you’re thinking about adopting Lean in your company, the easiest and most effective way to do so is by hiring a consultancy to do it for you. While Lean will require you to get everyone within the company to participate in order to get the most out of it, the best way to go about that can be challenging to find. Moreover, maintaining employee engagement in Lean culture can be even more challenging. If you have any questions about what we here at MJV can do to help, why not reach out to one of our consultants? Remember, you don’t have to go it alone.