Process Modeling: how to promote continuous improvement?
Modeling business processes is critical for optimizing operations and preparing for scalability.
Process modeling is a tool that helps teams and departments lay the groundwork for culture change within an organization. The idea is to help companies increase productivity, efficiency, and scalability through a continuous improvement mindset.
Does process modeling is for you? So, read the full article and
What is Process Modeling?
Business process modeling (BPM) is the systemic process of identifying, understanding, detailing, representing, and validating an organization’s processes.
- Processes, as a set of correlated and interdependent activities that converge towards a common objective.
- Process models are the organization, representation, and detailing of the resources and activities involved in the process.
BPMs are about operational workflow and can represent either a process model in its current state (as-is) or a possibly improved future state (to-be). Often depicted with a diagram, Process Models are intended to provide more process transparency.
→ Further reading
Process Consulting: understand the benefits for your business
The principles of Process Modeling
→ Standardization and compliance
→ Continuous process improvement
→ Avoid excessive automation
→ Process actor integration
→ Simplicity in process design
The benefits of Process Modeling
Among the most common benefits of process modeling, are increased productivity, agility, and cost reduction. But the advantages don’t stop there.
- Elimination of bottlenecks and friction points
- Reduction of rework
- Elimination of waste
- Optimization of time spent on tasks
- Greater process transparency and understanding
- Improved communication
- Preparation for automation
How to start Process Modeling?
Before starting the process diagram, it is important to stick to some prerequisites to ensure its adherence.
Select a survey approach
To successfully implement process modeling, you need to structure the flowchart with accurate activity information and data. It’s crucial that you select the right approach to carry out this survey.
Note that the nature of the information collection matters. There are three ways to do this:
Top-down: In this approach, a broader survey of the information and characteristics of processes is carried out first. Using this, a more detailed view is built from the most general to the most specific.
Middle-out: A model whose focus is to collect data on friction, failures, and problems within tasks and flows. This information will make up the basis for the process model.
Bottom-up: This strategy begins with the detailing of information and activities whose specificities within the processes are diagrammed primarily in relation to an overview.
Service Design is widely known for aiding in business investigation and understanding, as well as identifying points for improvement within processes.
Other methodologies such as Design Thinking are excellent for information collection. Through tools such as in-depth interviews, shadowing, and generating sessions, teams can gain a greater understanding of stakeholder expectations in relation to factors such as deliveries, possible frictions, and overall process alteration.
Choose a notation method
A notation method is nothing more than a language used to describe processes, a collection of symbols and rules.
Each notation has a specific purpose, varying according to the complexity of the representation, the approach used (top-down, bottom-up, or middle-out), as well as certain requirements or resources.
Among the most popular notations are:
- Business Process Modeling Notation (BPMN)
- Event Process Chain (EPC)
- Unified Modeling Language (UML)
- Integration Definition (IDEF)
Consolidate documentation
For a company to scale sustainably, workflows need to be properly assimilated by process actors. The keyword here is alignment.
This means that every aspect of the model, including phases, points of friction, solutions, and any other type of relevant detail, must be adequately documented.
This document will illustrate the decision-making process and guide the iteration cycles for process improvement. The language should be easy to understand among all stakeholders.
→ Content you may like
RPA: raise your business competitiveness
Six Steps to Effective Process Modeling
Here are MJV’s tips on making your models more effective, resilient, and less susceptible to failure.
1. Have a well-defined objective
What is your team’s definition of success? Define what the process must have in order to be efficient and productive.
2. Understand the process value chain
Understand how and when processes yield value. Map out all actors (and beneficiaries), discover how process execution and resolution affect them, and project the process’s importance within the company’s value chain.
3. Define process scope
Two prevalent mistakes are processes that are too complex or too simple.
Establishing a scope that is too large for a given process can stifle it. On the other hand, leaving gaps in understanding can lead to misinterpretations during execution.
The ideal is to find a functional balance for the level of detail within a process: not so brief that information is missing, nor so detailed that it impedes execution.
4. Have a beginning, middle, and end
Make sure that the steps and milestones within your model are clear and logical. Organize the model into smaller processes (sub-processes). But be careful not to fall into the trap of over-detailing.
5. Review and co-participation
In efforts to build an incremental improvement cycle, we strongly suggest continuous process monitoring and frequent reviewing, especially when measuring the model’s results in practice.
It’s always good to get a second opinion. Bring in your peers to inspect the model for gaps and suggest improvements.
6. Validation with process actors
Finally, it is time for trial by fire: the validation of the model’s adherence with the process actors. This tip follows the same principle as the previous phase: bring in people to support the decision-making process.
Modeling is useless if it doesn’t provide expected results for the executors of a process.
If this happens, seriously consider revisiting the model and iterating new versions using the feedback collected.
Build a routine of continuous improvement
The main goal of Process Modeling is not creating a new shiny version of an outdated process. Its benefits lie in the continuous incremental improvements that it provides for process designers and users. The true purpose of Process Modeling is to spread this approach among employees as a mindset, and institute gradual and concrete culture change.
One of the main uses for Process Modeling is laying the groundwork for automation, something we didn’t really have time to go in-depth in here. If you’re curious about how different process improvement procedures can pave the way for automation, why not take a look at some of our articles?
The final piece of advice we can give you is to seek specialized help. Starting a brand new initiative within your business can be a difficult process, but remember: you don’t have to go it alone. Go far, go with MJV.
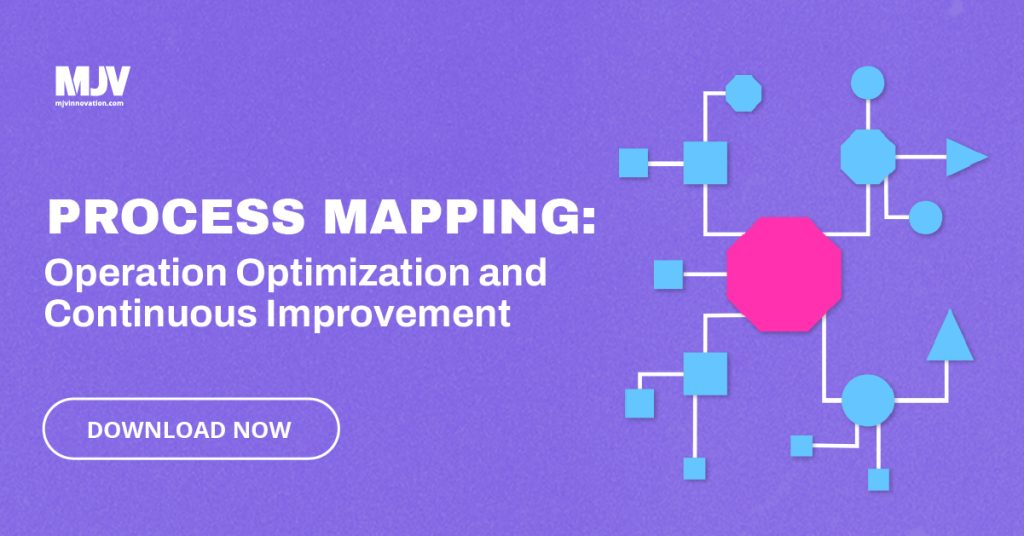